INK & STITCH SOLUTIONS
Elevate Your Brand with Custom Screen-Printing and Embroidery Services!
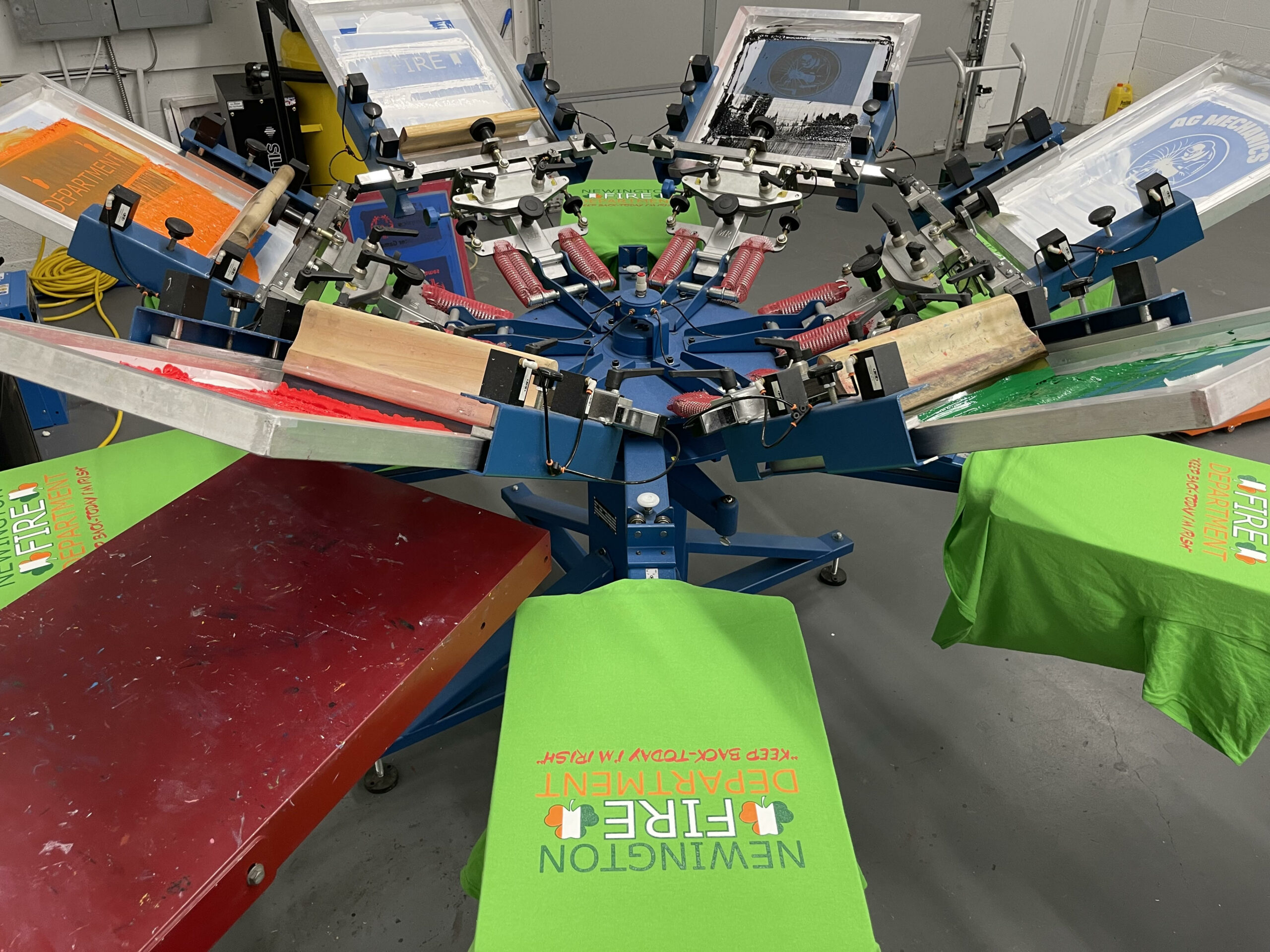
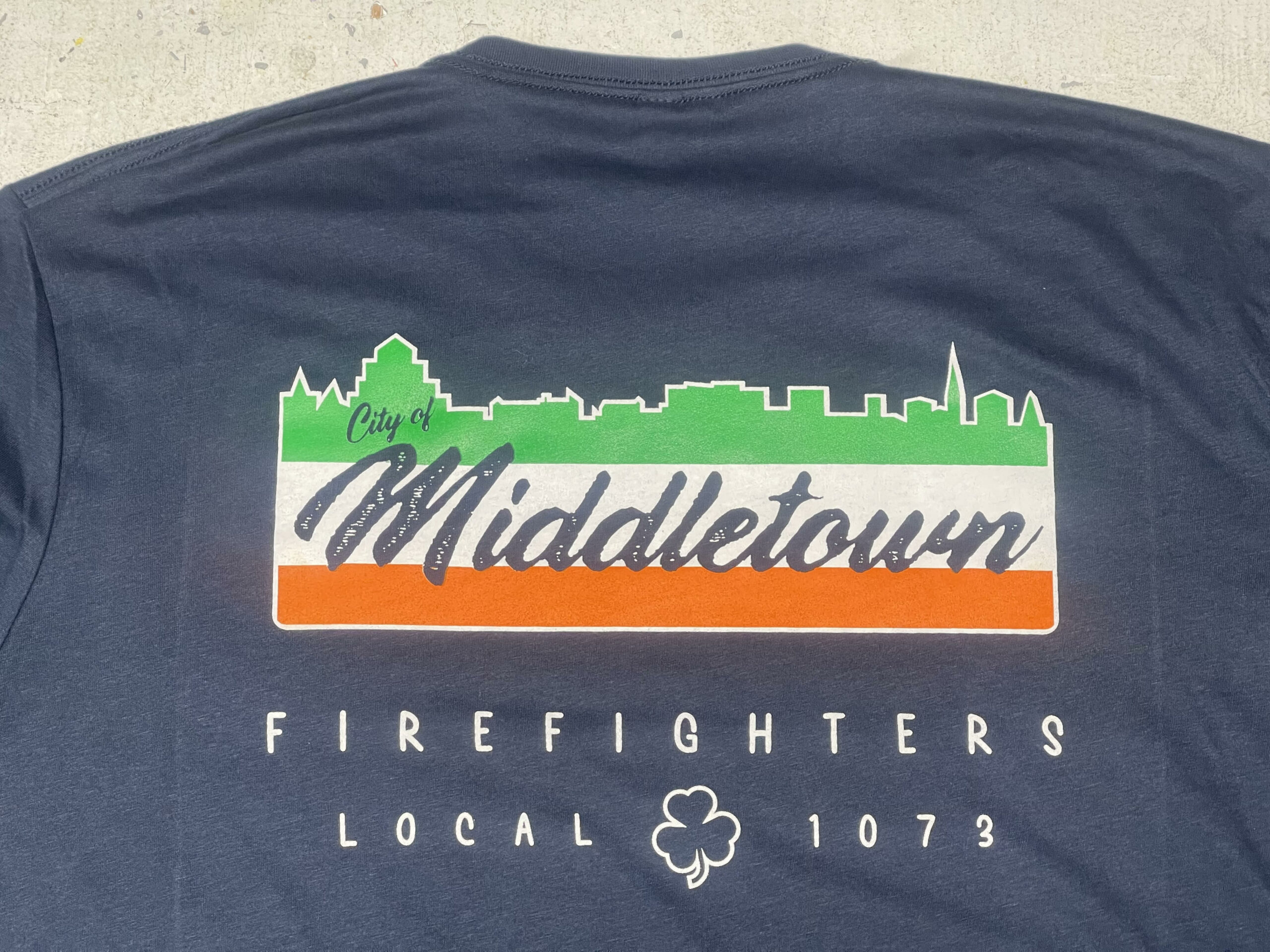
WHAT IS SCREEN-PRINTING?
The short answer:
Screen-printing is a special process that deposits ink onto an item in the design of your choice.
The long(er) answer:
Screen-printing involves creating a stencil (or “screen”) of your desired design on a fine mesh material, which is then stretched over a frame.
To print, the screen is placed over the item, and ink is applied to the top of the screen. A squeegee is then used to press the ink through the mesh, transferring the design onto the fabric below. This process can be repeated with different screens and colors to create multi-colored designs. The item is then passed through a heating unit to dry and set the ink. Screen-printing can be accomplished by hand, one at a time, or in our case, using a hand-fed machine that is capable of 400 shirts per hour.
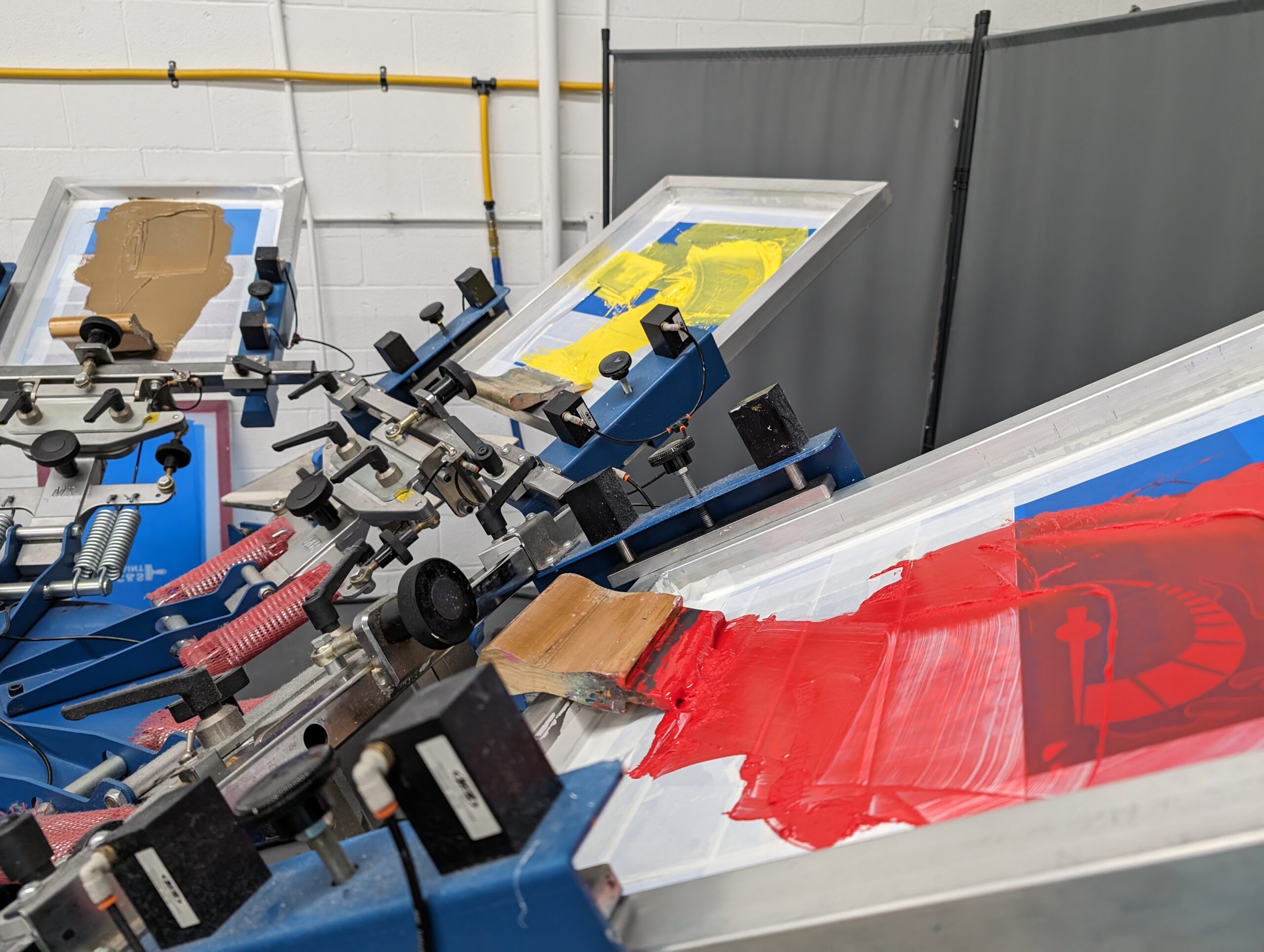
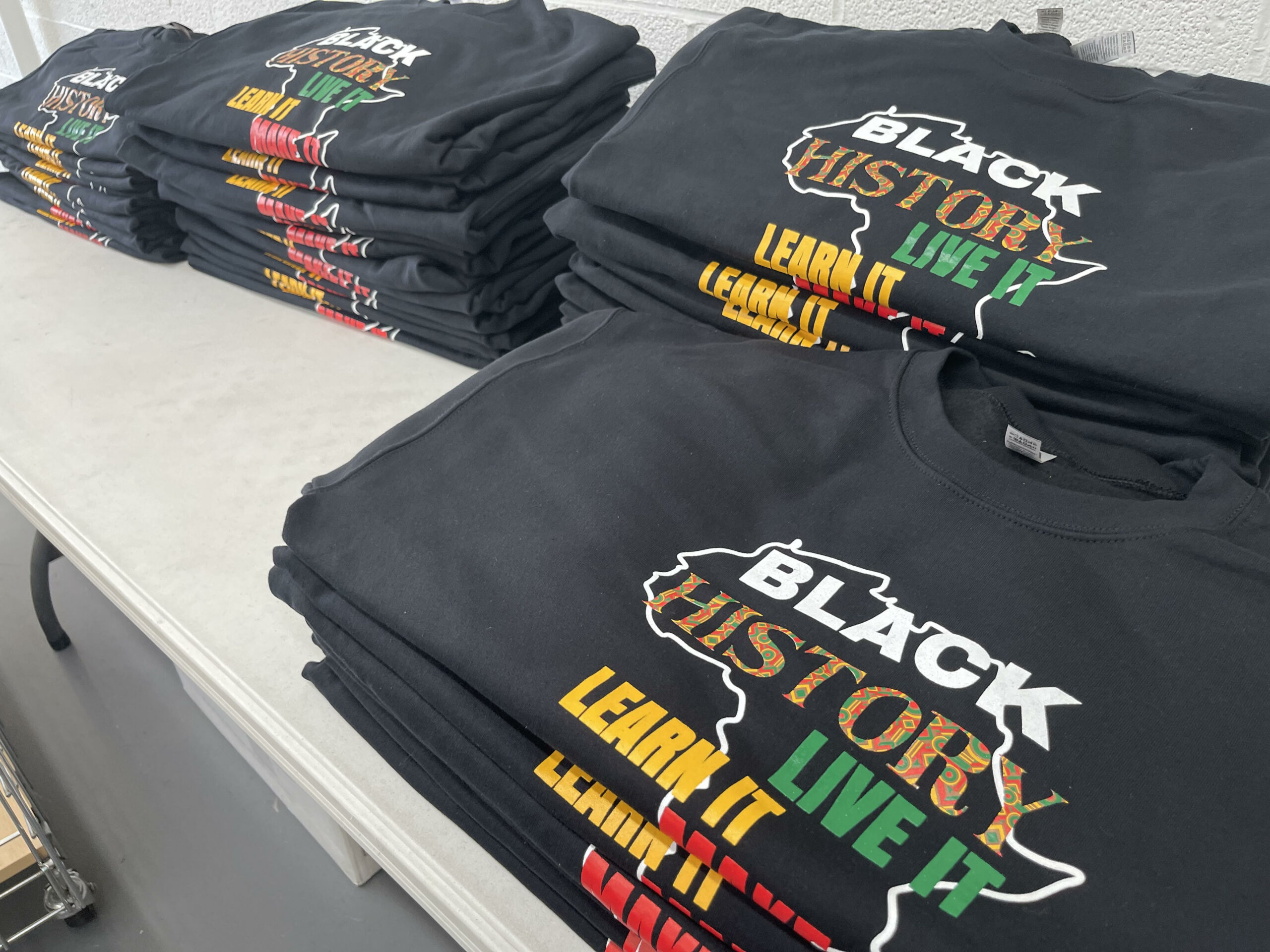
Screen-Printing is the Perfect Option For:
» Large orders
The per-piece price is reduced with volume, making screen-printing a very cost-effective way to print large quantities.
» Durability
Screen-printing is known for its durability, especially when compared to other printing methods like heat transfer or direct-to-garment printing. The ink used in screen-printing is thicker and more opaque, which helps it to adhere well to the fabric and withstand repeated washing and wearing. With proper care, screen-printed designs can last for a long time without fading or cracking.
» Versatility
Screen-printing can be done on a wide range of fabrics, including cotton, polyester, and blends, making it suitable for various types of apparel. The process produces high-quality, detailed designs with crisp edges, making it suitable for intricate artwork and text. Finally, your design can be customized within a single order to use different colors or placements on different types of apparel or items.
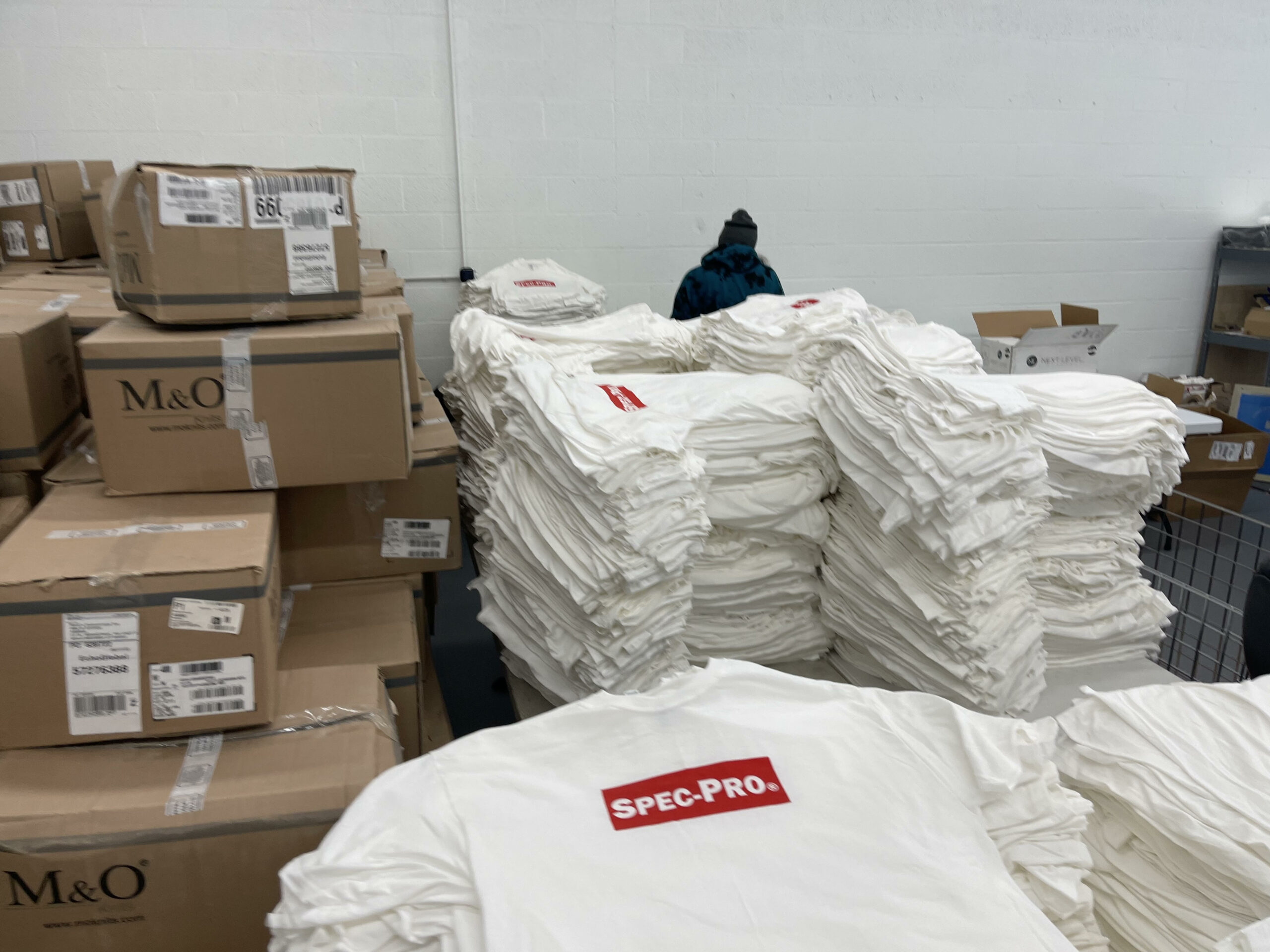
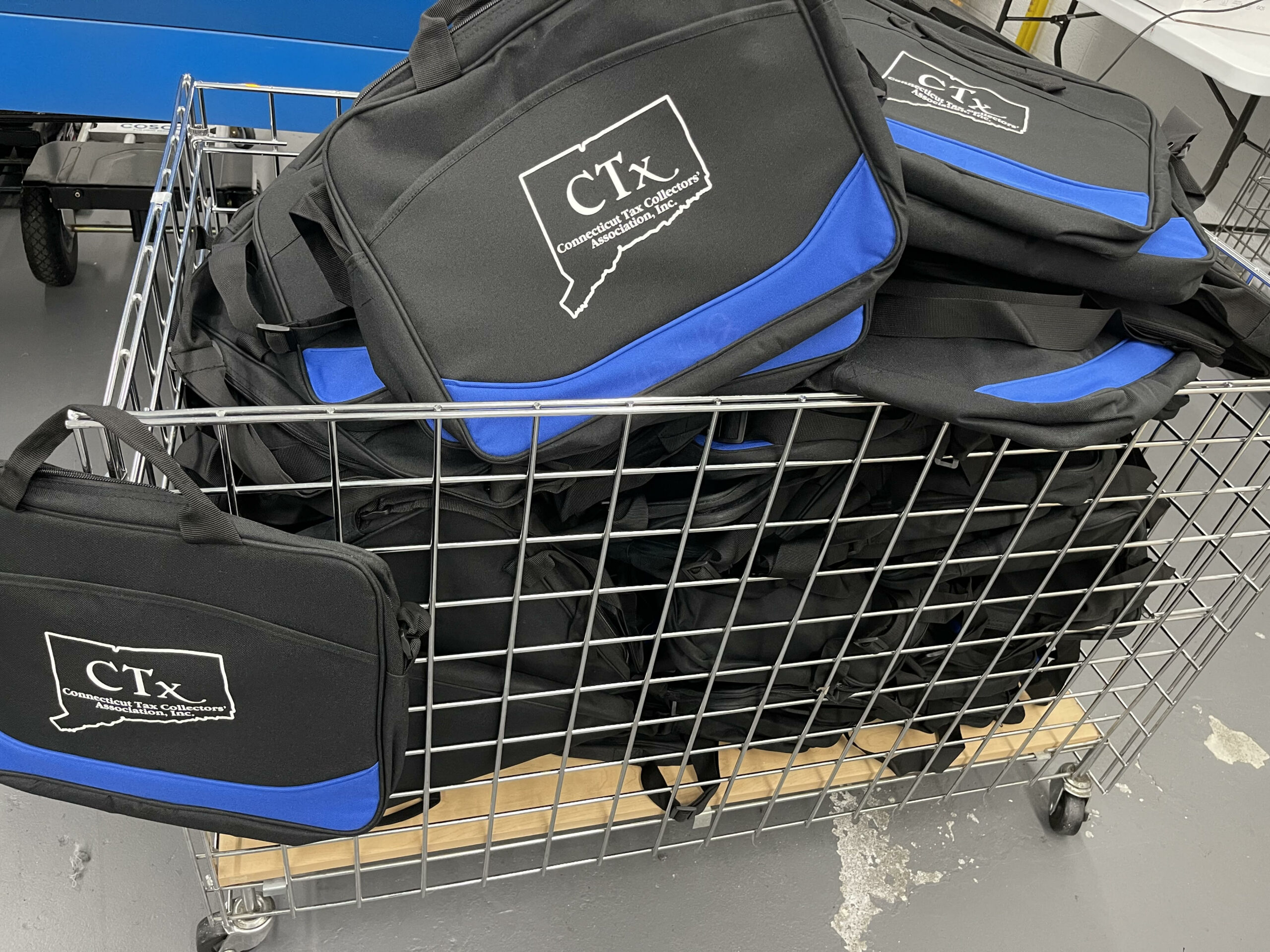
FREQUENTLY ASKED QUESTIONS
Is there a minimum order?
Yes. The minimum printing quantity for screen-printing is 12 pieces (of the same design). You can mix and match different types of apparel as long as the size and colors of the design remain the same. Screen-printing is not the most cost-effective way to personalize smaller orders, however, and the price-per-piece is less expensive for larger orders.
What do you need for Artwork?
For screen-printing, a vector file (.ai) of your artwork is required. If you do not have a vector file, you can submit your artwork to us in a JPG, PNG, SVG or PDF format and we can digitize the file for an additional fee.
What if I don't have artwork or my artwork needs editing?
If you do not have artwork or if your current artwork needs minor edits, we can help you to create your vision. Artwork development or editing fees are based on size and level of detail.
What are "setup" fees?
Every time you place a screen-printing order, you will incur setup fees to create and stretch the screens, mix the ink and set the machines. These fees are based on number of colors, sizes and locations. Each color, size and location require one unique screen. For example, you would like your 4-color logo to be printed on sweatshirts on the left chest (approximately 4″), the full back (approximately 10″) and the right sleeve. The imprint on the right sleeve will only be one color. You will incur the following setup fees:
Left chest x 4 colors = 4 screens x $30 = $120
Full back x 4 colors = 4 screens x $30 = $120
Right sleeve x 1 color = 1 screen x $30= $30
Total Setup Fees: $270
Why does the color of the apparel/item affect the pricing?
When painting, you would never attempt to cover dark walls with white paint without first using a primer.
When printing on dark colors, we use a “flash” process that is similar to priming. By flashing a white underbase before printing the final colors on a dark surface, the white ink can achieve better coverage and brightness, ensuring that the colors on top appear vibrant and true to their intended shade. This two-step process costs slightly more than projects that do not require a flash.
Can I provide my own apparel/items for screen-printing?
Due to the nature of the screen-printing process, there are occasions when items are damaged or mis-printed. As a result, we cannot take responsibility for items that are brought into us for screen printing. We have access to several distributors and brands for quality apparel and promotional items at competitive pricing. We prefer that all items be purchased through us, however in the rare occasion that we accept outside apparel, the customer accepts the risk that their items might be damaged without replacement.
Do you provide sub-contracting services for other businesses?
Yes! We currently work with several businesses as a sub-contractor, providing screen-printing and embroidery services to expand their service offerings to their customer base. There are many reasons why your business might choose to work with us as your sub-contracted screen-printer or embroidery professional:
1. Your physical location does not have the space or capacity for screen-printing or embroidery machine setups.
2. Your customers are interested in screen-printing or embroidery but you do not have the knowledge of the techniques and processes to achieve professional results worthy of your business name.
3. You do not have the time or staffing resources to dedicate to expanding into these areas.
4. You understand that working with a professional screen-printer or embroidery team adds value to your business and customers.
If you are interested in adding screen-printing and/or embroidery to your business, we would love to work with you and provide a quote for services. For more information please reach out to us at info@inkandstitchsolutions.com.
21 North Plains Industrial Road
Wallingford, Connecticut 06492
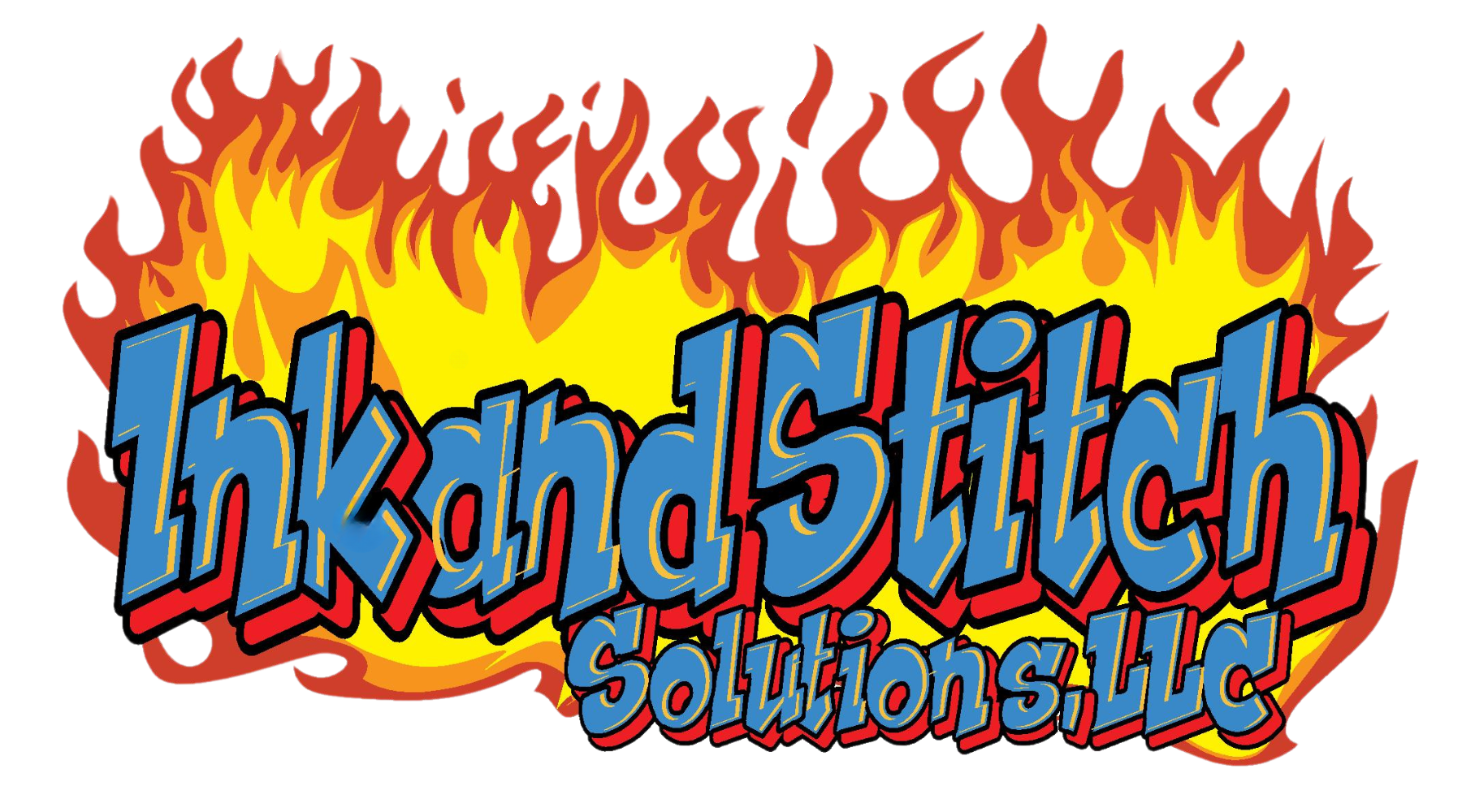
Open Monday through Friday
9:00am - 5:00pm